Insights: Taking Pre-Engineered Metal Buildings (PEMB) to a Higher Level
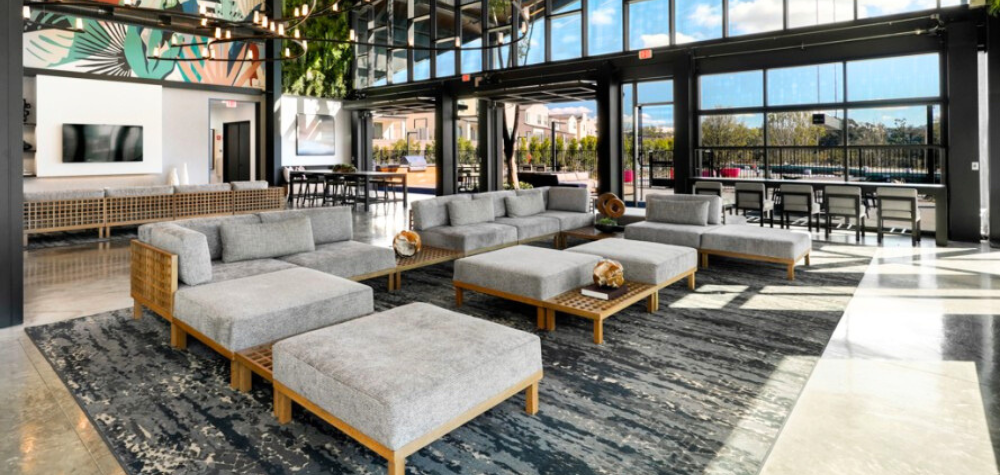
In today’s design and construction industry clients are seeking ways to ensure design accountability, cost accuracy, and delivery of a project to be proud of that leaves a signature footprint. We know the expectations of “speed to market” on retail, hospitality, commercial, and industrial space builds. The evolution of Pre-Engineered Metal Buildings (PEMB) in the design build platform has taken a more profound seat in a building type choice for these market areas. PEMB are becoming more popular as builders pursue options with decreased construction time and a greater level of structural integrity in their roofing and building systems. PEMB’s provide a superior alternative to traditional building types because there is less cost involved and less construction time. In some cases, a design build firm can also produce the structural design in-house and work in collaboration with the steel providers as a certified builder.
With a PEMB structural steel framing system, the fabrication work is performed offsite and delivered to the job site in ready-to-assemble pieces. Because they’re pre-fabricated and arrive ready-to-assemble, the base frame of the system helps contractors and developers maximize efficiency. In many cases these building types can also take architectural shape with style and creative design. The build can be enhanced with curtain walls, storefront adds, stucco, stone, and other architectural finish metals that give the facility an attractive appeal.
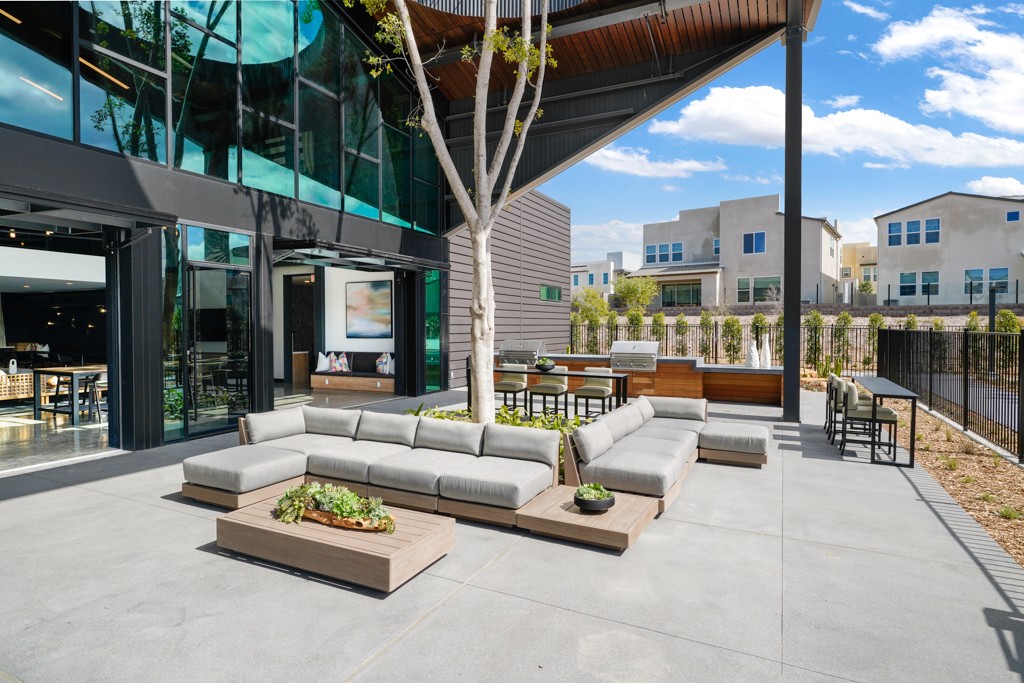
C&S recently completed a project for Lennar Communities (3Roots) where the PEMB was established as a “potential building type” option through a progressive design build delivery method selection. This delivery method allowed the C&S design build team to create building type options by massing the building on size, appearance, and finishes within this new residential housing community. The design portion also included verifying that the size was right for the expected demands during peak season at the gym and pool. The choice of PEMB was made based on multiple factors given style, blend, cost and time efficiency. The stakeholders for leasing this building space also were engaged to validate portions of the programming and design. This process allowed for the creation of a well-purposed space for wellness, events, and space in conjunction with the pool areas. While this project also included fabricated steel in specific areas, the PEMB acted as our mainframe and baseline skeleton for the structure. The structural steel additions were for bi-folding door assemblies, pop-out features, and locker room enhancements.
Will a PEMB Work for Your Needs? Here is What to Consider:
Cost. The steel is optimized to use the minimum amount of material at each location along the frame length. This leads to an estimated 30% savings on material – and by delivering C&S, transportation costs are also reduced. Costs associated with pre-engineered buildings are also more predictable than those of conventionally constructed buildings, allowing owners to have a more accurate picture of their investment.
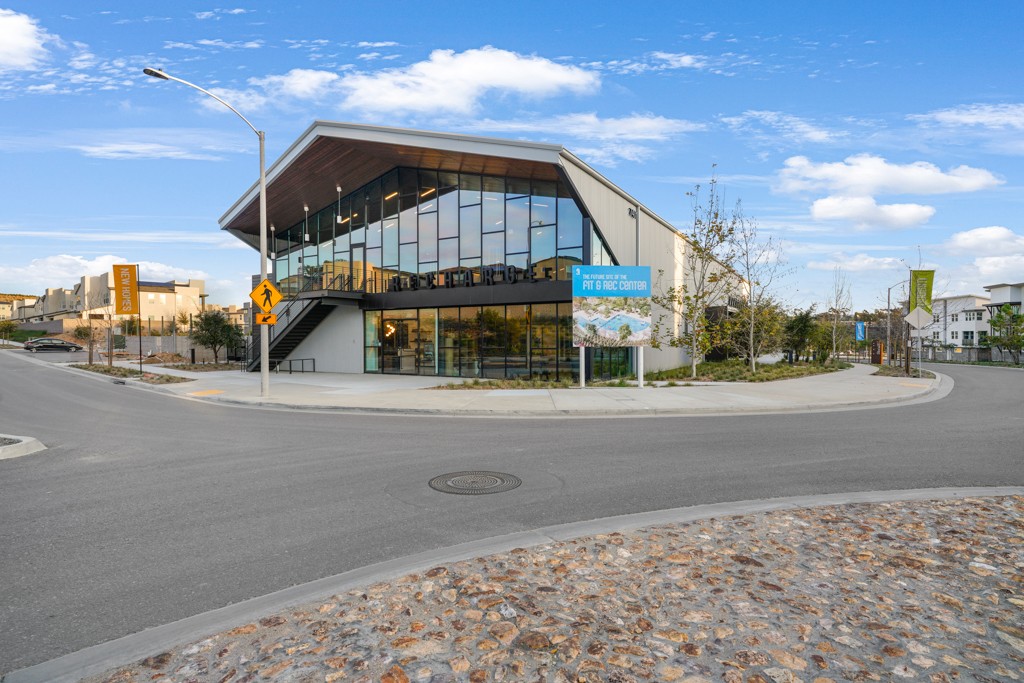
Sustainable & Minimized Environmental Footprint. Because pre-engineered buildings use less steel than conventionally built buildings, the environmental impact of PEMBs are also less. Pre-engineered buildings are energy efficient and provide optimum temperature control with no air leakage. Building walls can regulate heat with less insulation than conventional buildings and roofing systems can be engineered to reduce solar glare as needed.
Construction Time. Pre-engineered building components arrive ready to assemble with no welding or cutting required, so they can be assembled on average 50% faster than the construction time needed for conventional steel buildings. On the Lennar project we did have removal of some standard items included in the PEMB, so always be mindful to include cost for potential fabrication on-site.
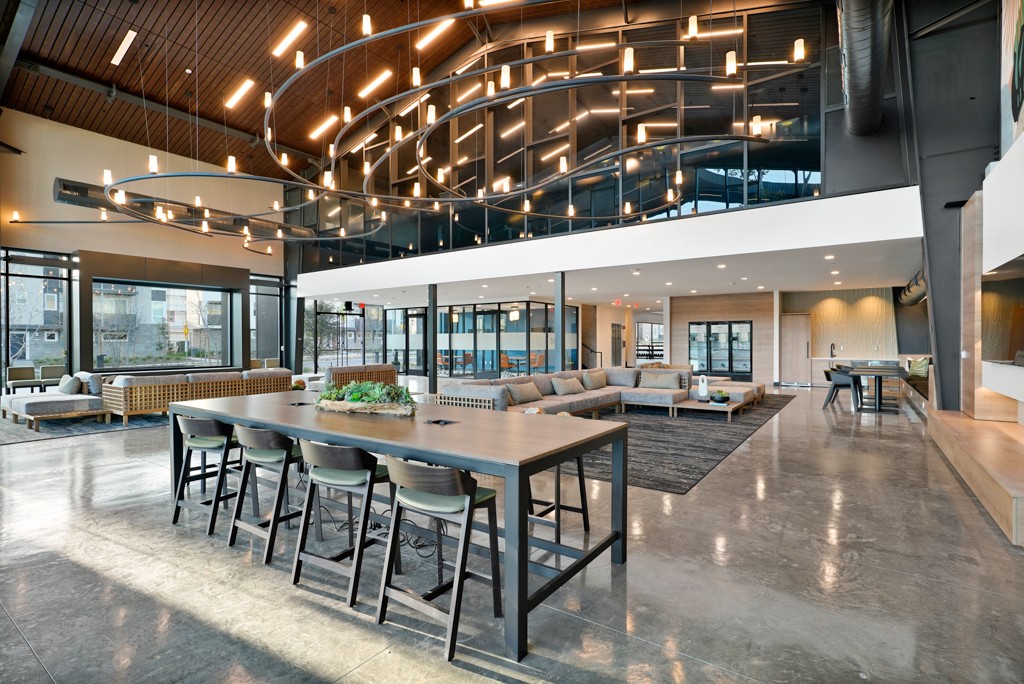
Customization. “Pre-engineered” doesn’t mean all buildings look the same. A wide variety of building materials offer many options to create unique looks to meet any requirements. PEMBs also create an open interior space that can be configured to meet almost any need. Even with customization, all components will be compatible because of the pre-engineered process.
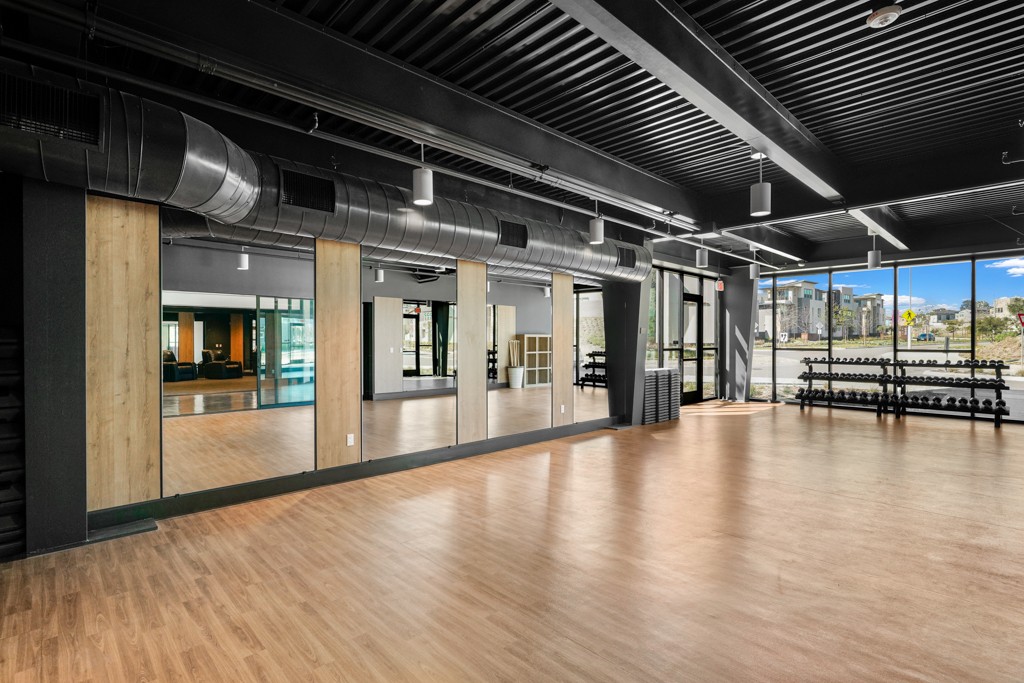
Scalability & Future Expansion. Pre-engineered building systems make it easy to expand as businesses grow and space needs change, because new sections can simply be added to the side or top of an existing building. Additionally, space for future expansion can be included as a design consideration of the original pre-engineered building.
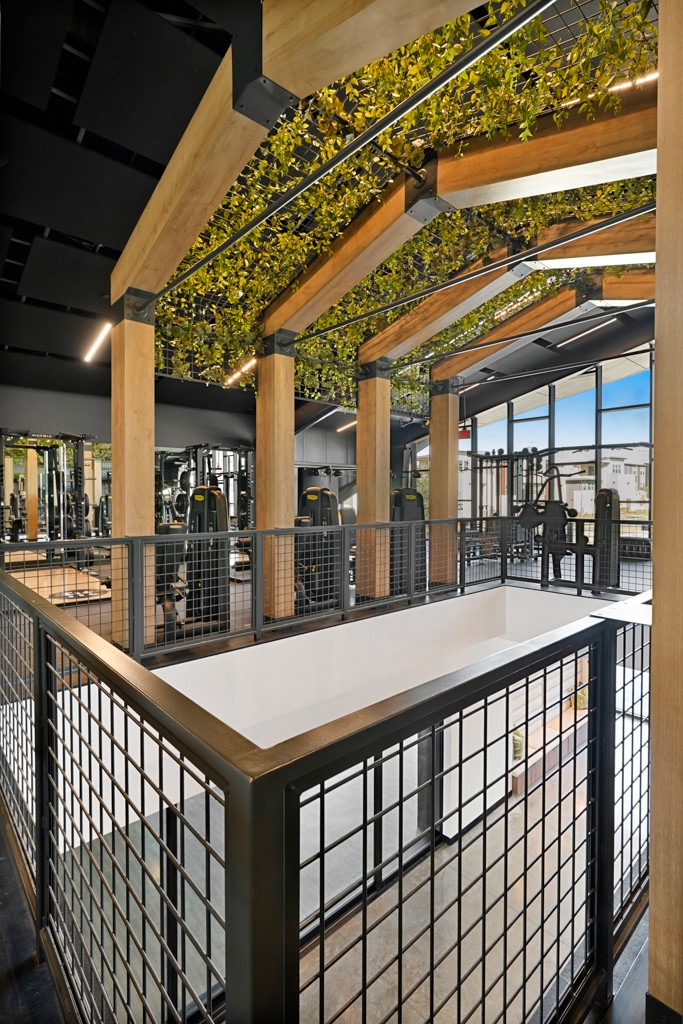
Structural Integrity. Structural steel is extremely strong, making it the leading choice for commercial and industrial buildings. Because steel frames offer high seismic resistance, pre-engineered buildings can withstand extreme weather conditions like hurricanes, tornadoes, and blizzards. PEMB roofing systems are also engineered to meet location-specific snow load requirements. Research and development groups within our company test and certify all of our components and materials.
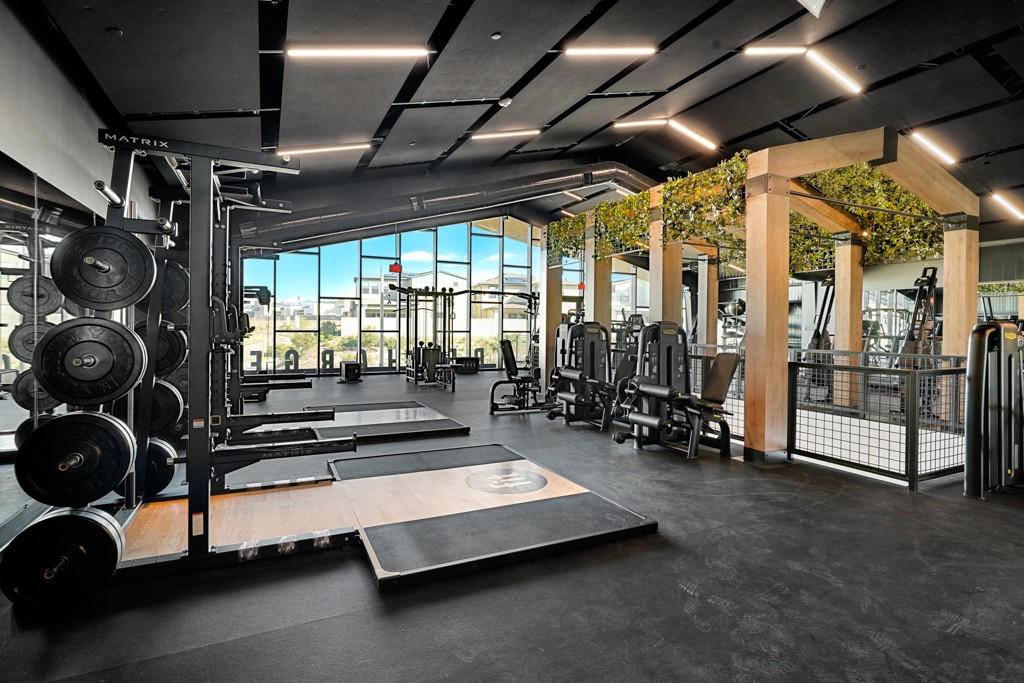
Larger Spans. Warehouse space and aircraft hangars are always in high demand for PEMB type. The larger spans are necessary for these types of buildings. The unique structure of pre-engineered buildings makes it possible to create larger clear spans with less structural steel.
Easy Maintenance. If needed, repairs to a building section can be done efficiently and with replacement parts direct from our manufacturing facility. Metal sidings can also be upgraded during the life span of the building.
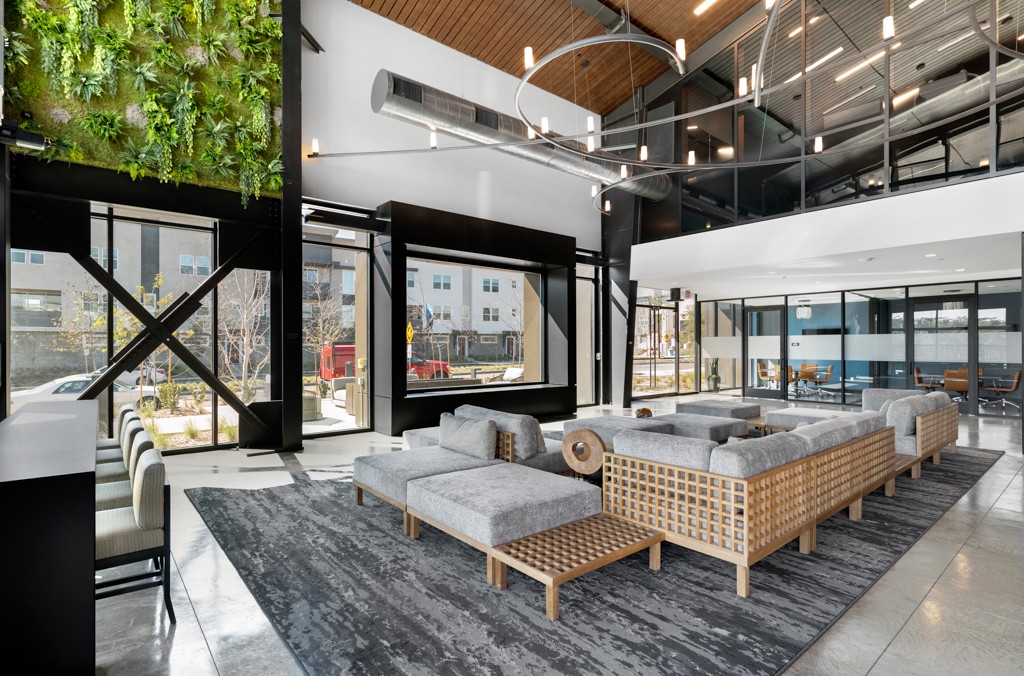
Long-Term Cost Savings. Ultimately, the structural integrity, streamlined maintenance, scalability, and reduced environmental impact of structural steel pre-engineered buildings save building owners significant time and money over the lifetime of the building.
If you’re considering the options of a PEMB, please ensure your design and contractor have vetted this building type as we will continue to see more in the marketplace as budgets get tight and interest rates raise, but demands are still in play. A PEMB can lead to a very attractive, efficient, and cost-friendly building. If you are interested in more information, please contact Cory Hazlewood at chazlewood@cscos.com.
Cory Hazlewood, DBIA, Vice President